In a world where efficiency is the lifeblood of success and waste is the silent killer of profits, there exists a methodology that promises to transform businesses and organizations into lean, mean, profit-producing machines. Imagine a system that combines the precision of a surgeon's scalpel with the power of a sledgehammer, aiming to eliminate errors, reduce costs, and maximize quality.
Lean Six Sigma, a secret weapon of some of the world's most successful companies, is not just a data-driven methodology; it's a revolution in how we approach business processes. Whether you're an executive, a manager, or simply someone with a curious mind, Lean Six Sigma is the key to unlocking the secrets of peak performance.
This article will look into the heart of this transformative force. We'll cover Lean Six Sigma principles, the keys to successful Six Sigma projects, and the benefits you can expect to enjoy.
What Is Lean Six Sigma?
Lean Six Sigma is a data-driven process improvement methodology and project management structure that combines two powerful approaches: "Lean," which focuses on reducing waste and inefficiency, and "Six Sigma," which aims to minimize defects and variations in processes. This combined approach is used to streamline operations, enhance quality, and increase organizational efficiency.
One of the earliest adopters of Lean Six Sigma was Motorola in the 1980s. They successfully reduced defects in their manufacturing processes, and it is said that their efforts saved over $16 billion. Their breakthrough inspired many other manufacturing companies, like General Electric, which credits Lean Six Sigma projects with saving them billions and improving product quality. It soon became a cornerstone of operational excellence in the manufacturing industry, proving that it wasn't just a passing trend.
In healthcare, where patient safety is paramount, Lean Six Sigma has played a crucial role. By streamlining processes and reducing errors, some organizations enhance patient satisfaction and reduce costs. This shows how Lean Six Sigma's principles could be applied outside traditional business settings, revolutionizing healthcare management and patient outcomes.
Even the financial sector, often associated with complex transactions, embraced Lean Six Sigma. A notable example is Bank of America, which used Lean Six Sigma to streamline its mortgage operations. They reduced processing times, minimized errors, and improved customer service. This demonstrated the adaptability of Lean Six Sigma principles across diverse sectors, proving its effectiveness in optimizing financial services.
The Six Sigma Methodology
The DMAIC process in Lean Six Sigma (Define, Measure, Analyze, Improve, Control) is vital for structured problem-solving and continuous improvement. It provides a systematic approach to identifying issues, measuring their impact, analyzing root causes, implementing solutions, and maintaining long-term control over processes, ensuring sustainable results. DMAIC fosters data-driven decision-making, reduces errors, and maximizes efficiency, making it a cornerstone of Lean Six Sigma's success in achieving quality and process improvements.
Several best practices and Sigma tools support the effective implementation of DMAIC in the Lean Six Sigma methodology.
Clear Project Definition: Start with a well-defined problem statement and project scope in the "Define" phase. This clarity ensures that the team's efforts remain focused on the most critical issues and opportunities for improvement.
Data Collection and Analysis: In the "Measure" phase, gather relevant data systematically and ensure its accuracy. Employ statistical tools to quantify process performance, identify variations, and prioritize areas that need improvement.
Root Cause Analysis: During the "Analyze" phase, dig deep to identify the root causes of issues rather than addressing symptoms. Techniques like Fishbone diagrams and the "5 Whys" can help uncover underlying problems.
Solution Testing: In the "Improve" phase, pilot test proposed solutions on a small scale before full implementation. This minimizes risks and allows for adjustments before rolling out changes across the organization.
Change Management: Implementing improvements using the Lean method can face resistance. Effective change management strategies, such as involving key stakeholders and communicating the benefits of the changes, are essential in the "Control" phase to ensure sustainable results.
Continuous Monitoring: Develop control plans and establish Key Performance Indicators (KPIs) to monitor process performance over time. Regularly review data and conduct periodic audits to ensure that the improvements are maintained.
Cross-Functional Teams: Involve employees from different departments and levels of the organization in the Lean methodology. Their diverse perspectives can lead to more comprehensive problem-solving and better solutions.
Training and Education: Invest in training team members in Lean Six Sigma principles and using relevant tools and methodologies to ensure they have the skills needed for each phase of the DMAIC process.
Documenting the Process: Keep detailed records and documentation, ideally using Six Sigma software, at each stage to provide a clear trail of the project's progress and results. This aids in knowledge sharing and future reference.
Celebrate Success: Recognize and celebrate the achievements and contributions of the team and the positive impact of improvements. Broadcasting success can motivate team members and foster a culture of continuous improvement within the organization.
By following these best practices and using the Sigma tools, organizations can effectively implement DMAIC and drive sustainable process improvements using the Lean Six Sigma methodology.
What Is the Difference Between Six Sigma and Lean Six Sigma?
Lean Six Sigma combines two distinct methodologies.
Lean Manufacturing (1900s - 1950s): The concept of "lean" can be traced back to the early 20th century, particularly with the development of the Toyota Production System (TPS) in post-World War II Japan. Taiichi Ohno, a Toyota engineer, is often credited with pioneering the principles of reducing waste, improving efficiency, and enhancing overall quality in manufacturing processes. This concept gained international attention during the 1980s when authors like James Womack and Daniel Jones introduced it in their book, "The Machine That Changed the World."
Six Sigma (1980s - 1990s): Motorola is credited with developing Six Sigma in the 1980s. Engineer Bill Smith at Motorola pioneered this methodology to reduce product defects. The term "Six Sigma" reflects the goal of achieving a process with so little variability that it falls within six standard deviations from the mean. Six Sigma gained momentum when Jack Welch adopted it as a central part of General Electric's management strategy during the 1990s, making it famous worldwide.
Integration and Evolution: The integration of Six Sigma and Lean into Lean Six Sigma became prominent in the late 1990s and early 2000s. This integration was primarily a response to the realization that while Six Sigma was excellent at reducing defects, it didn't address efficiency and speed in the same way that Lean principles did. Lean focuses on reducing waste and increasing process flow. By combining the two methodologies, organizations could address both quality and efficiency simultaneously.
Over time, Lean Six Sigma has evolved to be more than just a process improvement methodology in manufacturing. It has applications in various industries, including healthcare, finance, and services. The historical context of Lean Six Sigma showcases a journey from its humble beginnings in manufacturing to becoming a comprehensive approach for improving processes, reducing costs, and enhancing quality across diverse sectors. Its adaptability and proven track record have cemented its place as a valuable tool for organizations seeking operational excellence.
Lean Six Sigma Principles
Lean principles focus on eliminating waste and improving process flow, while Six Sigma emphasizes reducing defects and variations. When combined using Lean Six Sigma, these principles create a holistic approach that optimizes efficiency and quality, resulting in streamlined, high-performing processes.
1. Focus on the Customer
The Lean Six Sigma principle of "Focus on the customer" underscores the importance of understanding and meeting customer needs and expectations. It involves actively listening to customer feedback, identifying their requirements, and aligning processes and improvements to deliver products or services that provide the highest value and satisfaction to the end user. This customer-centric approach not only enhances product or service quality but also strengthens customer loyalty and trust, ultimately driving long-term business success.
2. Measure the Value Stream and Find Your Problem
Measuring the value stream involves systematically analyzing and mapping the entire process, from start to finish, to identify areas of waste, inefficiency, and defects. By measuring the value stream, organizations gain a comprehensive understanding of the current state of their processes, enabling them to pinpoint specific problems or bottlenecks that hinder productivity, quality, or customer satisfaction. This step serves as a foundational element in the Lean Six Sigma methodology, as it helps to target and prioritize improvements that will have the most significant impact on overall performance and customer value.
3. Remove Waste to Create Flow
This Lean Six Sigma principle emphasizes the systematic elimination of non-value-added activities or waste from processes to achieve smooth and efficient workflow. By identifying and reducing unnecessary steps, delays, or resources that do not contribute to the end product or service, organizations can optimize their operations, reduce costs, and deliver value to customers more swiftly and consistently
4. Eliminate Variations
Eliminating variations involves reducing and controlling process variations to enhance consistency and quality. Variations can lead to defects, inefficiencies, and customer dissatisfaction. By systematically identifying and addressing the sources of variation, organizations can ensure that their processes operate within tight tolerances and produce more predictable and reliable results, ultimately leading to higher product and service quality and greater customer satisfaction.
5. Undertake Improvements in a Systematic Process
Lean Six Sigma emphasizes the structured and data-driven approach to making process improvements within an organization. It involves following a defined methodology, such as DMAIC, to identify, analyze, and implement changes systematically and methodically. This approach ensures that improvements are well-founded, based on evidence and analysis, and that their impact can be measured and sustained over time, leading to more consistent and effective enhancements in processes and performance.
6. Equip People in Processes
It is critical to empower employees by providing them with the necessary skills, knowledge, and tools to participate in and contribute to process improvement efforts actively. By involving and training individuals at all levels of the organization, Lean Six Sigma fosters a culture of continuous improvement. This principle acknowledges that people on the front lines often have valuable insights into process inefficiencies and can be the driving force behind positive change when adequately equipped with the skills and resources to identify and address issues.
7. Understand the Real Work Flow
The Lean Six Sigma principle of "Understand the Real Work Flow" emphasizes the need to gain a deep and accurate understanding of how work processes truly function in practice. Getting to the actual workflow involves going beyond theoretical or idealized representations of operations and, instead, directly observing and studying how tasks are executed, how information flows, and where potential bottlenecks or inefficiencies exist. By comprehensively grasping the actual workflow, organizations can make more informed decisions about process improvements and better align their efforts with the practical realities of their operations, leading to more effective and sustainable changes.
Lean Six Sigma Phases of Business Transformation
The DMAIC improvement cycle, a fundamental framework within the Lean Six Sigma methodology, consists of five stages, each with tools and techniques to support it. DMAIC software is frequently used to structure the team's work.
Define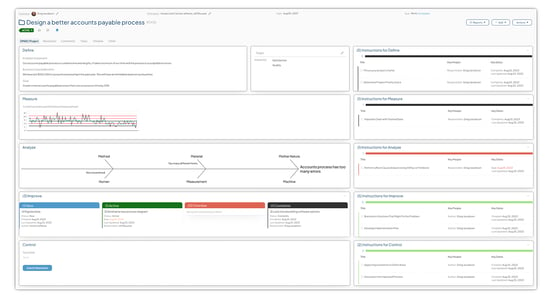
In this initial phase, the project's objectives are clearly defined. This includes outlining the problem, setting specific goals, and creating a project outline that sets the scope, resources, and the project team.
The key objective is to establish a clear understanding of the problem and its impact on the organization, ensuring that everyone involved is on the same page and working towards a common goal.
The Lean Six Sigma tools used at this stage include:
Project Charter: Summarizes the project's scope, goals, team members, and stakeholders.
Voice of the Customer (VOC) Analysis: Captures customer needs and expectations.
Measure
During the "Measure" phase, the current state of the process is assessed. Measurement involves collecting relevant data and metrics, creating process maps to visualize the workflow, and determining the process capability.
The goal is to establish a baseline of how the process is currently performing, identifying any deviations from desired performance standards.
The following techniques are used to support this phase:
Data Collection Plan: Outlines how data will be gathered.
Process Maps: Visual representations of the current process.
Statistical Analysis: Tools like descriptive statistics and hypothesis testing.
Analyze
In this stage of the Lean methodology, the collected data is analyzed in-depth to identify the root causes of the problem. The aim is to pinpoint the fundamental reasons behind the issues and prioritize which factors must be addressed for improvement.
Popular analysis tools include:
Cause-and-effect Diagrams (Ishikawa or Fishbone Diagram): Identifies potential causes of issues.
Root Cause Analysis: Techniques such as the "5 Whys."
Data Analysis: Statistical methods to pinpoint the main contributors to problems.
Improve
The "Improve" phase focuses on developing and implementing changes to resolve the root causes identified in the previous stage. It involves brainstorming ideas, redesigning processes, and conducting experiments to test potential improvements.
The objective is to find and apply solutions that will result in a more efficient and effective process, ultimately eliminating or minimizing the issues.
Improvement is supported by:
Brainstorming and Idea Generation: Generate potential solutions.
Process Redesign: Restructure processes to eliminate waste and improve efficiency.
Design of Experiments (DOE): Systematically test solutions.
Control
In the "Control" phase, the improvements are integrated into the standard processes. Control requires establishing control charts and systems to monitor performance, documenting new procedures (Standard Operating Procedures or SOPs), and ensuring that employees are trained and equipped to sustain the improvements.
The primary goal is to maintain the gains achieved during the project and prevent regression to the previous state.
Useful tools and techniques to maintain control include:
Control Charts: Monitor and maintain process stability.
Standard Operating Procedures (SOPs): Documented and accessible procedures for standard work.
Training and Communication Plans: Ensure changes are well-implemented.
Lean Six Sigma Belt Levels
Lean Six Sigma uses a "belt" system to designate levels of expertise and responsibilities within the methodology. The Six Sigma belt levels, from lowest to highest, are as follows:
White Belt: This is the entry-level designation. White Belts typically have a basic understanding of Six Sigma concepts and may be involved in local problem-solving teams. They assist Yellow Belts, Green Belts, and Black Belts in projects.
Yellow Belt: Yellow Belts have a foundational knowledge of Six Sigma principles. They work on project teams and support process improvements within their areas. Their role is often to collect data, assist with problem analysis, and implement solutions.
Green Belt: Green Belts are more advanced and take on more prominent roles within Six Sigma projects. They lead smaller projects, conduct data analysis, and work closely with Black Belts. They usually have full-time jobs outside of their Six Sigma responsibilities.
Black Belt: Black Belts are leaders of Six Sigma projects. They have extensive training in statistical methods and problem-solving techniques. They can lead and mentor Green Belts, facilitate cross-functional teams, and are responsible for significant process improvements.
Master Black Belt: These individuals are Six Sigma experts with extensive experience. They provide leadership, mentoring, and training to Black and Green Belts. They often work on high-level strategic projects and help organizations implement Six Sigma across various departments.
These Six Sigma belt levels help organizations structure their Lean Six Sigma efforts, with each group representing a different degree of expertise and responsibility in process improvement.
Benefits of Lean Six Sigma
Lean Six Sigma is widely used as a continuous improvement framework because it is a repeatable, scalable approach that offers significant benefits to organizations of all types and sizes.
Increased Efficiency and Productivity
Lean Six Sigma increases efficiency and productivity by identifying and eliminating waste and process defects. It streamlines operations, reduces unnecessary steps, and optimizes workflows. Through data-driven analysis and continuous improvement, it not only enhances quality and customer satisfaction but also reduces costs, ultimately leading to more efficient and productive processes within an organization.
Improved Quality
The approach improves quality by systematically identifying and eliminating errors, defects, and process variations. It analyzes the root causes of quality issues, allowing for targeted improvements. Lean Six Sigma enhances process consistency and efficiency, leading to higher-quality products and services, ultimately resulting in improved customer satisfaction.
Employee Engagement and Development
Lean Six Sigma leads to employee engagement and development by involving employees in problem-solving and improvement efforts. It empowers them to contribute to the organization's success, fostering a sense of ownership and pride in their work. Additionally, the training and skill development offered as part of Lean Six Sigma equips employees with valuable tools and knowledge, further enhancing their professional growth and engagement in the organization.
Reduced Costs
The Lean Six Sigma method reduces costs by identifying and eliminating waste and inefficiencies in processes, resulting in lower operational expenses. It targets areas where resources are underutilized, streamlines workflows, and minimizes defects, reducing rework and material costs. Eliminating waste leads to improved cost control and enhanced profitability for organizations.
Increased Customer Satisfaction
Lean Six Sigma increases customer satisfaction by improving the quality and consistency of the product or service. It identifies and eliminates errors and defects, leading to higher reliability and meeting customer expectations. Additionally, streamlined processes lead to quicker delivery and better customer service, ultimately enhancing the overall customer experience and satisfaction.
How Much Does It Cost to Get Lean Six Sigma Training?
The cost of Lean Six Sigma training can vary widely depending on factors such as the level of training, the training provider, and the specific program or certification you're pursuing.
Online training courses are usually more affordable than classroom-based training. They can range from a few hundred dollars to a few thousand dollars, depending on the level of training, the belt rank of the trainee, and the provider.
In addition to training, certification fees may apply, which can range from $300 to $800 or more, depending on the certifying body and the level of certification.
It's essential to research different training providers, compare their offerings, and consider your specific needs and goals when determining the cost of Lean Six Sigma training. Additionally, some organizations offer in-house training, which can have varying costs depending on the scale and customization of the program.
(Conclusion): Transforming Businesses with Lean Six Sigma
The value of Lean Six Sigma lies in its ability to enhance organizational efficiency, quality, and profitability systematically. By fostering a culture of continuous improvement, it empowers businesses to meet customer demands, reduce waste, and maintain a competitive edge in a rapidly evolving global marketplace.
Embracing Lean Six Sigma in your organization isn't just a choice; it's a strategic imperative. By implementing these principles, you pave the way for efficient, high-quality processes that drive customer satisfaction and fuel your competitive advantage. Don't just consider it—take the leap and experience the transformational power of Lean Six Sigma for lasting process improvement and success.
How KaiNexus Can Help
If you have any Lean Six Sigma tips or best practices to add to the discussion, please comment on this post. This is also a great way to pose questions to the continuous improvement community.
If you are ready to start your Lean Six Sigma journey, KaiNexus can help. Contact one of our improvement experts today to learn more about how your organization can spread, sustain, and measure the impact of your improvement culture.
Add a Comment